在制藥行業中,十萬級GMP無菌灌裝車間是確保藥品安全性和有效性的關鍵環節。這類車間按照國際通行的GMP(藥品生產質量管理規范)標準建設,通過嚴格的空氣凈化系統、人員操作規范和環境監控措施,將生產環境中的微生物和塵埃粒子控制在每立方米不超過10萬個的級別(即ISO8級),從而滿足無菌制劑生產的特殊要求。特別是十萬級車間的核心設計要注意這些要素。
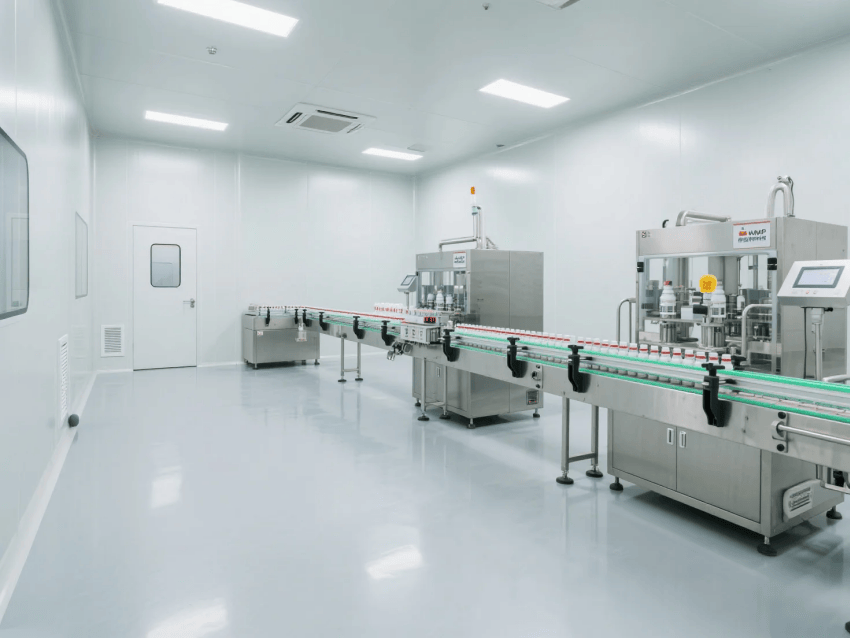
1.**空氣凈化系統**
車間的核心在于高效空氣過濾(HEPA)系統的應用。通過初效、中效和高效三級過濾,可去除99.97%以上粒徑≥0.3μm的顆粒物。網易新聞報道的某生物制藥企業案例顯示,其灌裝車間采用頂送側回的氣流組織方式,形成單向流保護區域,確保灌裝線附近的局部潔凈度達到更高標準(如ISO5級)。
2.**環境參數控制**
百度百科資料指出,十萬級車間需維持溫度20-24℃、濕度45%-65%的恒溫恒濕狀態,壓差梯度設計需保證空氣從潔凈區向非潔凈區單向流動。某企業通過實時監測系統聯動空調機組,實現動態調節,確保環境穩定性。
3.**材料與設備選擇**
不銹鋼材質是灌裝設備的首選,因其耐腐蝕、易清潔的特性。據行業報道,現代灌裝機普遍配備隔離器或RABS(限制進出屏障系統),通過自動化減少人員干預。如某疫苗生產企業采用全封閉灌裝線,將人為污染風險降低90%以上。
十萬級無菌灌裝車間的建設與運營,是制藥工藝、質量控制與工程技術的深度融合。隨著QMS(質量管理系統)的智能化升級和新型滅菌技術的應用,未來無菌保障水平將邁向新高度。但需注意,硬件投入僅是基礎,持續完善SOP(標準操作規程)和人員質量意識,才是確保藥品安全的長效機制。行業數據顯示,嚴格執行GMP的企業,其無菌制劑的市場投訴率可控制在百萬分之一以下,這充分證明了規范化管理的價值。